鋁合金氟碳漆施工工藝可保護鋁合金材料,提升其裝飾性與耐久性。以下是詳細的工藝流程:
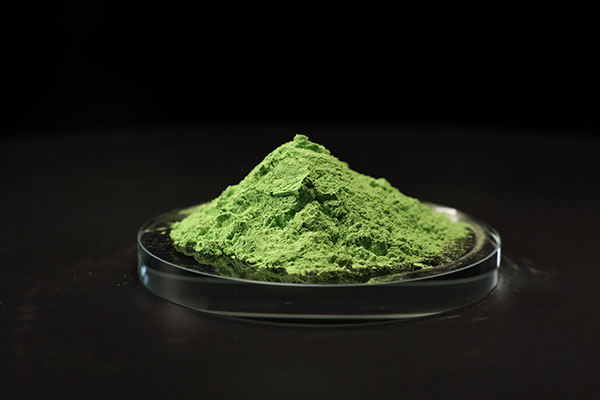
施工前準備
材料準備:
鋁合金基材:確保其質(zhì)量符合相關標準,表面應平整、無裂縫、無砂眼等缺陷。
氟碳漆:根據(jù)工程需求和設計要求,選擇質(zhì)量可靠、性能穩(wěn)定的氟碳漆產(chǎn)品。同時,配套準備相應的稀釋劑、固化劑等輔助材料,且這些材料應與所選氟碳漆具有良好的兼容性。
工具設備準備:
表面處理工具:包括電動角磨機、砂紙、鋼絲刷等,用于對鋁合金基材表面進行打磨、除銹等處理。
噴涂設備:常用的有空氣噴涂槍、高壓無氣噴涂機等。空氣噴涂槍適用于對裝飾性要求較高的場合,能夠獲得均勻、細膩的漆膜;高壓無氣噴涂機則適用于大面積施工,具有較高的噴涂效率和較好的漆膜質(zhì)量。同時,還需準備相應的空壓機、氣管、噴槍清洗設備等輔助工具。
測量工具:如膜厚儀、粗糙度儀等,用于在施工過程中對漆膜厚度、基材表面粗糙度等進行測量和監(jiān)控,確保施工質(zhì)量符合要求。
施工環(huán)境準備:
溫度:施工環(huán)境溫度應保持在5℃-35℃之間。當溫度過低時,氟碳漆的干燥速度會明顯減慢,甚至可能出現(xiàn)無法干燥的情況,影響漆膜的性能和質(zhì)量;當溫度過高時,漆液的溶劑揮發(fā)速度過快,容易導致漆膜表面出現(xiàn)橘皮、針孔等缺陷。
濕度:空氣相對濕度應控制在85%以下。濕度過高時,空氣中的水分容易在鋁合金基材表面凝結(jié),影響氟碳漆與基材的附著力,同時也可能導致漆膜在干燥過程中出現(xiàn)發(fā)白、起泡等現(xiàn)象。
通風:施工場所應保持良好的通風條件,以確??諝庵械钠犰F和溶劑蒸汽能夠及時排出,降低施工環(huán)境中的有害物質(zhì)濃度,保障施工人員的身體健康,同時也有利于漆液的干燥和固化,提高漆膜的質(zhì)量。
鋁合金表面處理
脫脂處理:鋁合金表面通常會有油污、油脂等污染物,這些污染物會影響氟碳漆與基材的附著力,因此需要進行脫脂處理。常用的脫脂方法有有機溶劑脫脂、堿性溶液脫脂和乳化液脫脂等。
有機溶劑脫脂:利用有機溶劑對油脂的溶解作用來鋁合金表面的油污。常用的有機溶劑有丙酮、丁酮、甲苯、二甲苯等。有機溶劑脫脂的優(yōu)點是脫脂速度快、效果好,對各種油脂都有較好的溶解能力;缺點是有機溶劑易燃易爆,具有的毒性,對環(huán)境有污染,且成本較高。在使用有機溶劑脫脂時,應注意通風良好,避免明火和靜電,操作人員應佩戴防護手套、口罩和護目鏡等防護用品。
堿性溶液脫脂:通過堿性溶液與鋁合金表面的油污發(fā)生皂化反應和乳化反應,將油污。常用的堿性溶液脫脂劑主要由氫氧化鈉、碳酸鈉、磷酸三鈉、硅酸鈉等堿性物質(zhì)和表面活性劑組成。堿性溶液脫脂的優(yōu)點是脫脂效果好,成本較低,對環(huán)境的污染相對較小;缺點是堿性溶液對鋁合金有的腐蝕性,尤其是在高溫、高濃度和長時間浸泡的情況下,容易導致鋁合金表面出現(xiàn)腐蝕坑、變色等缺陷。因此,在使用堿性溶液脫脂時,應嚴格控制脫脂液的濃度、溫度和浸泡時間,一般脫脂液的濃度為3%-10%,溫度為50℃-80℃,浸泡時間為5-20分鐘。脫脂后,應立即用大量清水沖洗鋁合金表面,將殘留的脫脂液沖洗干凈,然后進行中和處理,以防止鋁合金表面生銹。
乳化液脫脂:乳化液脫脂是利用乳化劑的乳化作用,將鋁合金表面的油污分散在水中形成乳濁液,從而達到油污的目的。乳化液脫脂劑主要由乳化劑、有機溶劑、緩蝕劑、助溶劑等組成。乳化液脫脂的優(yōu)點是脫脂速度快、效果好,對各種油脂都有較好的乳化能力,且對鋁合金的腐蝕性較小;缺點是乳化液脫脂劑的成本相對較高,且乳化液中的有機溶劑易燃易爆,對環(huán)境有的污染。在使用乳化液脫脂時,應注意控制乳化液的濃度、溫度和浸泡時間,一般乳化液的濃度為2%-5%,溫度為40℃-60℃,浸泡時間為10-30分鐘。脫脂后,應立即用大量清水沖洗鋁合金表面,將殘留的乳化液沖洗干凈。
酸洗處理:經(jīng)過脫脂處理后的鋁合金表面,可能還會殘留一些氧化皮、銹跡等雜質(zhì),這些雜質(zhì)會影響氟碳漆與基材的附著力,因此需要進行酸洗處理。酸洗處理是利用酸溶液與鋁合金表面的氧化皮、銹跡等雜質(zhì)發(fā)生化學反應,將其溶解,從而使鋁合金表面露出新鮮的金屬表面,提高氟碳漆與基材的附著力。常用的酸溶液有硫酸、鹽酸、硝酸、磷酸等。在選擇酸溶液時,應根據(jù)鋁合金的材質(zhì)、表面狀態(tài)和雜質(zhì)種類等因素進行綜合考慮,選擇合適的酸溶液和酸洗工藝參數(shù)。
硫酸酸洗:硫酸是一種常用的酸洗溶液,其優(yōu)點是價格便宜,貨源廣泛,對鋁合金表面的氧化皮、銹跡等雜質(zhì)有較好的溶解能力,且酸洗后鋁合金表面的光澤度較好。缺點是硫酸的腐蝕性較強,尤其是在高溫、高濃度的情況下,容易對鋁合金表面造成過度腐蝕,導致鋁合金表面出現(xiàn)腐蝕坑、變色等缺陷。因此,在使用硫酸酸洗時,應嚴格控制硫酸溶液的濃度、溫度和酸洗時間,一般硫酸溶液的濃度為10%-20%,溫度為40℃-60℃,酸洗時間為5-20分鐘。酸洗后,應立即用大量清水沖洗鋁合金表面,將殘留的硫酸溶液沖洗干凈,然后進行中和處理,以防止鋁合金表面生銹。
鹽酸酸洗:鹽酸也是一種常用的酸洗溶液,其優(yōu)點是對鋁合金表面的氧化皮、銹跡等雜質(zhì)有較強的溶解能力,尤其是對鐵銹的溶解速度較快,且鹽酸的揮發(fā)性較強,酸洗后鋁合金表面的殘留酸液容易揮發(fā),對后續(xù)的處理工藝影響較小。缺點是鹽酸的腐蝕性較強,對鋁合金表面有的腐蝕作用,尤其是在高溫、高濃度的情況下,容易導致鋁合金表面出現(xiàn)腐蝕坑、變色等缺陷。同時,鹽酸的揮發(fā)性較強,在酸洗過程中會產(chǎn)生大量的酸霧,對環(huán)境有污染,且對操作人員的身體健康有的危害。因此,在使用鹽酸酸洗時,應嚴格控制鹽酸溶液的濃度、溫度和酸洗時間,一般鹽酸溶液的濃度為5%-15%,溫度為30℃-50℃,酸洗時間為3-15分鐘。酸洗后,應立即用大量清水沖洗鋁合金表面,將殘留的鹽酸溶液沖洗干凈,然后進行中和處理,以防止鋁合金表面生銹。同時,應加強通風措施,減少酸霧對環(huán)境的污染和對操作人員身體健康的危害。
硝酸酸洗:硝酸是一種強氧化性酸,在鋁合金酸洗中,硝酸不僅可以溶解鋁合金表面的氧化皮、銹跡等雜質(zhì),還可以在鋁合金表面形成一層致密的氧化膜,提高鋁合金表面的耐腐蝕性和與氟碳漆的附著力。硝酸酸洗的優(yōu)點是酸洗速度快、效果好,對鋁合金表面的各種雜質(zhì)都有較好的溶解能力,且酸洗后鋁合金表面的氧化膜質(zhì)量較好,能夠提高鋁合金表面的耐腐蝕性和與氟碳漆的附著力。缺點是硝酸的腐蝕性較強,尤其是在高溫、高濃度的情況下,容易對鋁合金表面造成過度腐蝕,導致鋁合金表面出現(xiàn)腐蝕坑、變色等缺陷。同時,硝酸是一種強氧化性酸,在酸洗過程中會產(chǎn)生大量的氮氧化物氣體,對環(huán)境有嚴重的污染,且對操作人員的身體健康有的危害。因此,在使用硝酸酸洗時,應嚴格控制硝酸溶液的濃度、溫度和酸洗時間,一般硝酸溶液的濃度為5%-15%,溫度為30℃-50℃,酸洗時間為3-15分鐘。酸洗后,應立即用大量清水沖洗鋁合金表面,將殘留的硝酸溶液沖洗干凈,然后進行中和處理,以防止鋁合金表面生銹。同時,應加強通風措施,安裝廢氣處理設備,對酸洗過程中產(chǎn)生的氮氧化物氣體進行處理,達標后排放,減少對環(huán)境的污染和對操作人員身體健康的危害。
磷酸酸洗:磷酸是一種中強酸,在鋁合金酸洗中,磷酸對鋁合金表面的氧化皮、銹跡等雜質(zhì)有較好的溶解能力,且磷酸在鋁合金表面形成的磷酸鹽膜具有較好的耐腐蝕性和與氟碳漆的附著力。磷酸酸洗的優(yōu)點是酸洗速度相對較慢,對鋁合金表面的腐蝕作用較小,能夠避免鋁合金表面出現(xiàn)過度腐蝕的現(xiàn)象,且酸洗后鋁合金表面形成的磷酸鹽膜質(zhì)量較好,能夠提高鋁合金表面的耐腐蝕性和與氟碳漆的附著力。缺點是磷酸的價格相對較高,且磷酸的酸性相對較弱,對鋁合金表面的一些頑固雜質(zhì)的溶解能力可能不如硫酸、鹽酸等強酸。因此,在使用磷酸酸洗時,應根據(jù)鋁合金表面的具體情況和對酸洗效果的要求,合理選擇磷酸溶液的濃度、溫度和酸洗時間。一般磷酸溶液的濃度為10%-30%,溫度為50℃-80℃,酸洗時間為10-30分鐘。酸洗后,應立即用大量清水沖洗鋁合金表面,將殘留的磷酸溶液沖洗干凈,然后進行中和處理,以防止鋁合金表面生銹。
鉻化處理(可選):鉻化處理是在鋁合金表面形成一層鉻酸鹽轉(zhuǎn)化膜的過程。這層轉(zhuǎn)化膜具有良好的耐腐蝕性、性和與氟碳漆的附著力,能夠進一步提高鋁合金表面的防護性能和裝飾性能。鉻化處理的方法主要有浸漬法、噴淋法和刷涂法等,其中浸漬法是常用的方法。在進行鉻化處理時,應根據(jù)鋁合金的材質(zhì)、表面狀態(tài)和使用要求等因素,合理選擇鉻化液的配方、濃度、溫度和處理時間等工藝參數(shù)。
鉻化液配方:鉻化液的配方通常由鉻酸鹽、氟化物、氧化劑、還原劑、緩沖劑等組成。不同的鉻化液配方適用于不同的鋁合金材質(zhì)和表面狀態(tài),因此在選擇鉻化液配方時,應根據(jù)實際情況進行試驗和篩選,選擇合適的鉻化液配方。
鉻化處理工藝參數(shù):鉻化處理的工藝參數(shù)主要包括鉻化液的濃度、溫度、處理時間和pH值等。一般來說,鉻化液的濃度越高,溫度越高,處理時間越長,形成的鉻酸鹽轉(zhuǎn)化膜的厚度越厚,耐腐蝕性和與氟碳漆的附著力越好。但是,過高的濃度、溫度和處理時間也會導致鉻酸鹽轉(zhuǎn)化膜的質(zhì)量下降,如出現(xiàn)膜層疏松、龜裂、脫落等缺陷。因此,在進行鉻化處理時,應根據(jù)鋁合金的材質(zhì)、表面狀態(tài)和使用要求等因素,合理選擇鉻化液的濃度、溫度、處理時間和pH值等工藝參數(shù),一般鉻化液的濃度為3%-8%,溫度為30℃-50℃,處理時間為3-10分鐘,pH值為2-5。鉻化處理后,應立即用大量清水沖洗鋁合金表面,將殘留的鉻化液沖洗干凈,然后進行干燥處理,以防止鉻酸鹽轉(zhuǎn)化膜生銹。
干燥處理:經(jīng)過脫脂、酸洗和鉻化處理后的鋁合金表面,會殘留一些水分,這些水分如果不及時,會影響氟碳漆與基材的附著力,同時也可能導致鋁合金表面生銹。因此,在進行氟碳漆噴涂之前,需要對鋁合金表面進行干燥處理。干燥處理的方法主要有自然干燥、熱風干燥、烘干箱干燥等,其中熱風干燥是常用的方法。在進行熱風干燥時,應根據(jù)鋁合金的材質(zhì)、表面狀態(tài)和尺寸大小等因素,合理選擇熱風的溫度、風速和干燥時間等工藝參數(shù),一般熱風的溫度為50℃-80℃,風速為2-5m/s,干燥時間為10-30分鐘。干燥處理后,應檢查鋁合金表面的干燥程度,確保鋁合金表面無水分殘留。同時,應注意保持干燥后的鋁合金表面清潔,避免再次受到污染。
氟碳漆涂裝
底漆涂裝:底漆是氟碳漆涂層系統(tǒng)的基礎,其主要作用是增強氟碳漆與鋁合金基材的附著力,防止基材生銹,同時為面漆提供良好的表面基礎,使面漆能夠地附著和發(fā)揮其裝飾性能。常用的底漆有環(huán)氧底漆、聚氨酯底漆、丙烯酸底漆等,其中環(huán)氧底漆因其具有良好的附著力、耐腐蝕性和封閉性,是鋁合金氟碳漆涂裝中常用的底漆。
底漆調(diào)配:在進行底漆涂裝之前,需要根據(jù)所選底漆的產(chǎn)品說明書和施工要求,將底漆、固化劑和稀釋劑按照的比例進行調(diào)配。調(diào)配時,應先將底漆倒入干凈的容器中,然后按照產(chǎn)品說明書上規(guī)定的比例加入固化劑,用攪拌器充分攪拌均勻,使其充分反應。后,根據(jù)施工要求和底漆的粘度,適量加入稀釋劑,繼續(xù)攪拌均勻,使底漆的粘度達到施工要求。底漆的調(diào)配比例應嚴格按照產(chǎn)品說明書上的規(guī)定進行,不得隨意更改,以免影響底漆的性能和質(zhì)量。同時,調(diào)配好的底漆應在規(guī)定的時間內(nèi)用完,以免底漆發(fā)生固化反應,導致無法使用。
底漆涂裝方法:底漆的涂裝方法主要有空氣噴涂、高壓無氣噴涂、刷涂、滾涂等,其中空氣噴涂和高壓無氣噴涂是常用的方法。空氣噴涂是利用壓縮空氣將底漆霧化成細小的顆粒,然后通過噴槍將這些顆粒均勻地噴涂在鋁合金表面上??諝鈬娡康膬?yōu)點是噴涂效率高,能夠獲得均勻、細膩的漆膜,適用于對裝飾性要求較高的場合;缺點是對施工環(huán)境的要求較高,需要有良好的通風條件,同時漆霧的反彈和飛散會造成的浪費,增加施工成本。高壓無氣噴涂是利用高壓泵將底漆增壓至15-30MPa,然后通過噴槍的噴嘴將底漆噴出,在大氣壓力的作用下,底漆瞬間霧化成細小的顆粒,均勻地噴涂在鋁合金表面上。高壓無氣噴涂的優(yōu)點是噴涂效率高,能夠獲得較厚的漆膜,適用于大面積施工和對防護性能要求較高的場合;缺點是對施工設備的要求較高,需要配備高壓泵、噴槍等設備,同時由于底漆的壓力較高,對噴槍的操作要求也較高,如果操作不當,容易導致漆膜出現(xiàn)橘皮、流掛等缺陷。在選擇底漆的涂裝方法時,應根據(jù)鋁合金的材質(zhì)、表面狀態(tài)、尺寸大小、施工環(huán)境和對漆膜質(zhì)量的要求等因素進行綜合考慮,選擇合適的涂裝方法。同時,在進行底漆涂裝時,應嚴格按照所選涂裝方法的操作規(guī)程進行操作,確保底漆的涂裝質(zhì)量。
底漆干燥:底漆涂裝完成后,需要讓底漆進行干燥固化。底漆的干燥固化時間主要取決于底漆的類型、配方、施工環(huán)境溫度和濕度等因素。一般來說,環(huán)氧底漆的干燥固化時間在常溫下(25℃)需要12-24小時,在低溫下(5℃-15℃)需要24-48小時。在進行底漆干燥固化時,應注意保持施工環(huán)境的通風良好,避免施工環(huán)境中的濕度和溫度過高或過低,影響底漆的干燥固化速度和質(zhì)量。同時,在底漆干燥固化過程中,應避免對底漆表面進行碰撞、摩擦和污染,以免影響底漆的附著力和防護性能。底漆干燥固化完成后,應檢查底漆的干燥程度和附著力,確保底漆表面干燥、無氣泡、無針孔、無流掛等缺陷,且底漆與鋁合金基材的附著力良好,符合施工要求。如果底漆表面存在缺陷或附著力不符合要求,應及時進行處理,如對底漆表面進行打磨、修補,重新進行底漆涂裝等,直到底漆的干燥程度和附著力符合施工要求為止。
中間漆涂裝(可選):中間漆是氟碳漆涂層系統(tǒng)中位于底漆和面漆之間的一層漆,其主要作用是增加涂層的厚度,提高涂層的防護性能和裝飾性能,同時也可以對底漆表面的一些微小缺陷進行填充和修飾,使面漆能夠地附著和發(fā)揮其裝飾性能。在鋁合金氟碳漆涂裝中,是否需要涂裝中間漆應根據(jù)具體情況進行綜合考慮,如鋁合金的使用環(huán)境、對涂層防護性能和裝飾性能的要求、底漆的種類和性能等因素。一般來說,對于使用環(huán)境較為惡劣、對涂層防護性能和裝飾性能要求較高的鋁合金制品,如建筑幕墻、門窗、戶外家具等,通常需要涂裝中間漆;而對于使用環(huán)境較為溫和、對涂層防護性能和裝飾性能要求不是特別高的鋁合金制品,如一些室內(nèi)裝飾品、小型電子設備外殼等,可以不涂裝中間漆。
中間漆調(diào)配:如果需要涂裝中間漆,在進行中間漆涂裝之前,需要根據(jù)所選中間漆的產(chǎn)品說明書和施工要求,將中間漆、固化劑和稀釋劑按照的比例進行調(diào)配。調(diào)配方法與底漆調(diào)配方法基本相同,應先將中間漆倒入干凈的容器中,然后按照產(chǎn)品說明書上規(guī)定的比例加入固化劑,用攪拌器充分攪拌均勻,使其充分反應。后,根據(jù)施工要求和中間漆的粘度,適量加入稀釋劑,繼續(xù)攪拌均勻,使中間漆的粘度達到施工要求。中間漆的調(diào)配比例應嚴格按照產(chǎn)品說明書上的規(guī)定進行,不得隨意更改,以免影響中間漆的性能和質(zhì)量。同時,調(diào)配好的中間漆應在規(guī)定的時間內(nèi)用完,以免中間漆發(fā)生固化反應,導致無法使用。
中間漆涂裝方法:中間漆的涂裝方法與底漆涂裝方法基本相同,主要有空氣噴涂、高壓無氣噴涂、刷涂、滾涂等,其中空氣噴涂和高壓無氣噴涂是常用的方法。在選擇中間漆的涂裝方法時,應根據(jù)鋁合金的材質(zhì)、表面狀態(tài)、尺寸大小、施工環(huán)境和對漆膜質(zhì)量的要求等因素進行綜合考慮,選擇合適的涂裝方法。